Next-generation Amazon fulfillment center in Shreveport uses robots to boost efficiency, safety, and delivery speed alongside employees.
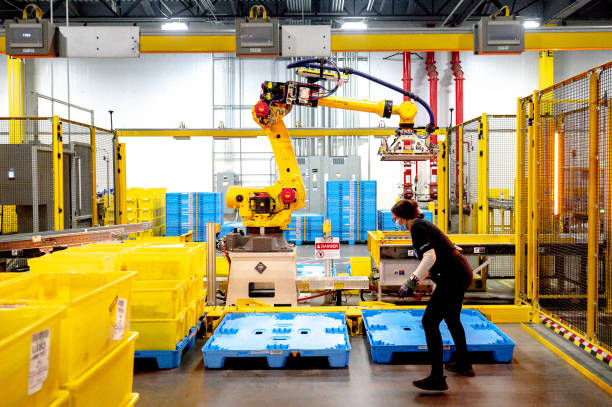
As customer expectations for fast, reliable delivery continue to rise, Amazon faces increasing pressure to meet these demands without compromising efficiency or safety.
The challenge is clear: how to speed up order fulfillment while protecting workers and minimizing costs. Amazon’s next-generation fulfillment center in Shreveport offers a solution.
By integrating advanced robotics that work alongside employees, Amazon is enhancing productivity, improving safety, and speeding up deliveries, setting a new standard for the future of logistics.
Next-Generation Amazon Fulfillment Center: Facility Features
Spanning five floors and over 3 million square feet (equivalent to 55 football fields), it is one of Amazon’s largest sites. The company says that this next-generation Amazon fulfillment center will employ 2,500 people at full ramp-up.
Advanced Technology Integration
Amazon’s next-generation fulfillment center leverages eight state-of-the-art robotics systems, seamlessly integrated with Amazon Web Services (AWS) cloud computing. These systems process data from sensors, cameras, and machines in real-time, ensuring optimal performance and efficiency.
Key highlights include:
- Advanced AI enables smooth collaboration between robotics and employees, enhancing productivity by an estimated 25%.
- The robotics suite is designed for deployment across Amazon’s network, modernizing logistics and streamlining fulfillment processes.
Amazon’s robotics technology aims to enhance employee safety, simplify tasks, and boost productivity while ensuring faster package deliveries to customers.
Robotics and AI In Next-Generation Amazon Fulfillment Center
In the next-generation Amazon fulfillment center, eight sophisticated robots work seamlessly to enhance package fulfillment, ensuring faster delivery and supporting employees in their tasks. Each robot has a unique role that contributes to the efficiency and productivity of the system.
1. Sequoia
Sequoia uses AI and robotics to optimize inventory storage, consolidating items quickly and efficiently. By transporting inventory directly to storage systems or employees, it increases storage speed by up to 75%, reducing fulfillment times and improving ergonomics for workers by placing items at ideal heights for easier access.
2. Hercules
Hercules moves pods of items across the fulfillment center to employees who pick products for customer orders. Using a 3D camera, it navigates independently, ensuring safety by detecting obstacles and differentiating between robots, people, and objects.
3. Titan
Titan is a heavy-duty drive unit that specializes in moving larger, bulkier items like household appliances or food pallets. It has the ability to lift twice the weight of Hercules, using computer vision to navigate the robotics floor efficiently.
4. Sparrow
Sparrow is a robotic arm that uses computer vision and AI to pick and place individual items into totes for order fulfillment. This system ensures precise item handling, streamlining the picking process for employees.
Globally, 60% of employees working with robotics and AI anticipate improvements in safety, career growth, and productivity.
MIT's Automation from the Worker’s Perspective
5. Packaging Automation
Once the items are selected, Amazon uses automated packaging systems that create custom paper bags, tailored to the order’s dimensions. This eco-friendly solution helps reduce plastic use and ensures sustainable, recyclable packaging for customers.
6. Robin
Robin is the first robotic arm deployed by Amazon to sort packages. It transfers packages from conveyor belts onto robotic drive units, ensuring quality control by rerouting damaged items and preparing packages for the outbound dock.
7. Cardinal
Cardinal, another robotic arm, uses AI and computer vision to quickly and accurately select packages from a chute, lifting them with air suction and placing them into carts for final delivery to the trucks. It handles packages up to 50 pounds, minimizing the risk of injury for employees.
8. Proteus
Proteus is Amazon’s first fully autonomous mobile robot, capable of navigating freely throughout the fulfillment center. It moves carts from the outbound area to the loading docks, coordinating with Cardinal to ensure smooth delivery operations.
Does This Mean Robots Will Replace Amazon's Human Employees?
According to the company, robots won’t replace humans at Amazon. Instead, advanced robotics create more opportunities for skilled jobs.
Fulfillment centers with this technology require 30% more employees in roles like reliability, maintenance, and engineering. Through programs like Career Choice and robotics apprenticeships, Amazon supports employees in earning certifications and advancing their careers, often with higher wages.
Sending Inventory to Amazon Fulfillment Center
When using Amazon’s Fulfillment by Amazon (FBA) service, sellers cannot choose which fulfillment center their products will be sent to. Amazon’s system determines the destination based on product type, demand, and regional distribution needs to optimize storage and delivery efficiency.
To send inventory to Amazon:
Access the “Send to Amazon” Workflow (STA). Navigate to the “Shipping Queue” under the Inventory tab in Seller Central and select “Send to Amazon.”
Prepare Shipment Information.
- Choose the inventory to send (ensure the SKUs are FBA-enabled).
- Provide the shipping address and marketplace destination.
- Specify packing details, whether individual units or case packs.
Confirm Shipping Details. Input estimated ship dates and select a carrier (Amazon-partnered or self-arranged). Estimated costs will be displayed for comparison.
Print Labels. Generate and print box or pallet labels. Ensure all labels are attached correctly to shipments.
Track Shipments. Once the carrier picks up the shipment, tracking updates in Seller Central help ensure smooth delivery to the assigned fulfillment center.
Finding Your Amazon Fulfillment Center and Inventory Warehouse
To find out where your FBA inventory is stored, follow the steps described in this video:
1. In Amazon Seller Central, click on the hamburger menu, then go to Reports > Fulfillment.
2. Select Inventory > Inventory Ledger.
3. Download Summary View Fulfillment Center report (choose CSV format for easier sorting) after setting the date range.
4. Open the downloaded CSV file and look under the “Location” column to see a list of your inventory locations across various warehouses.
Notice that the location data is presented in code form rather than an exact address. To identify the specific facility, sellers and Amazon Agrency alike can use this Amazon Fulfillment Center/Warehouse codes paired with their corresponding addresses.
Knowing which Amazon fulfillment center your products are shipped to is crucial for several reasons:
- Helps track inventory levels, ensuring timely restocking and avoiding stockouts.
- Assists in anticipating delivery times and managing customer expectations.
- Enables accurate calculation of storage fees, helping to reduce costs.
- Ensures shipments are sent to the correct centers, avoiding delays and fees.
- Facilitates efficient management of returns or removals.
- Provides accurate shipping information, improving customer satisfaction.
How Orders Are Packed In Amazon Fulfillment Centers
Amazon’s order packing and delivery process is a blend of advanced technology and a commitment to safety. When you place an order, robots bring the items to picking areas for processing. Adjustable workstations and smart tools ensure employees work comfortably and safely.
Packages move through a streamlined hub-and-spoke system for efficient sorting and transportation. At delivery stations, parcels are prepared for their final journey, with safety audits and ergonomic tools supporting drivers. Equipped with AI-driven safety cameras, delivery vehicles ensure secure and timely deliveries, bringing smiles to your door with care.